Betriebsmittelproduktivität verbessern – Beispiel: Handlungsfeld Instandhaltung
Betriebsmittelproduktivität verbessern – Beispiel: Handlungsfeld Instandhaltung
Die Betriebsmittelproduktivität steigern Sie mit allen Verbesserungsmaßnahmen, die den Zustand, die Qualität, den Leistungsgrad, die Nutzungsdauer und die Verfügbarkeit Ihres Maschinenparks positiv verändern und den gesamten Bereich der Anlagenwirtschaft optimieren. Dieser Abschnitt befasst sich mit der Instandhaltung als einem ausgewählten Bereich der Anlagenwirtschaft.
Von der Optimierung der Instandhaltung können Sie Verbesserungen folgender Teilproduktivitäten erwarten:
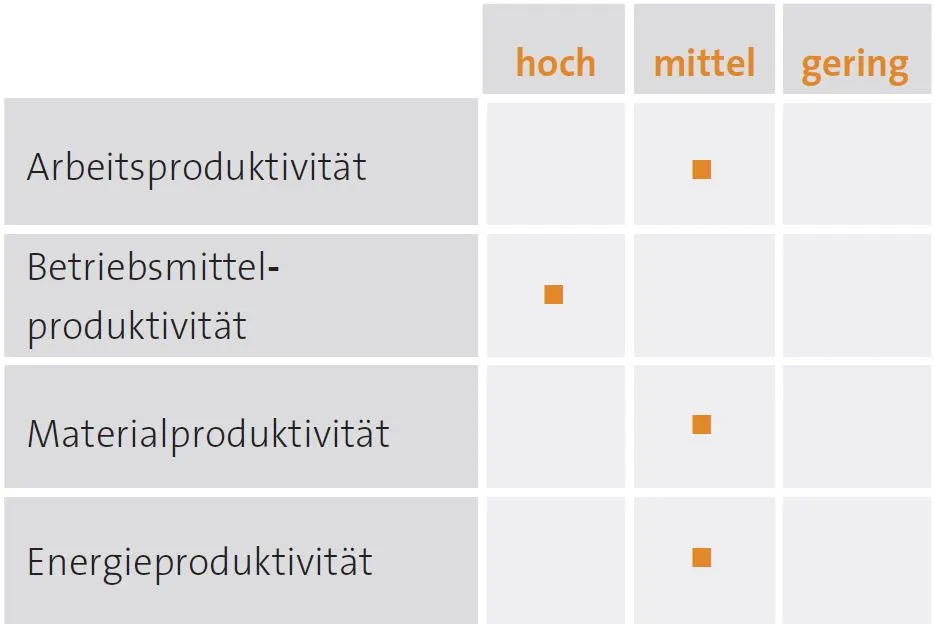
Störungen im Produktionsprozess sind prinzipiell nicht zu vermeiden. Sie können Störungsarten, Störungsumfänge und Störungskosten aber durch eine Vielzahl von betrieblichen Maßnahmen minimieren. In diesem Zusammenhang hat die Instandhaltung die Aufgabe, die Auswirkungen von Betriebsmittelstörungen so gering wie möglich zu halten. Eine wirksame Instandhaltung trägt deshalb wesentlich zu einer besseren Betriebsmittelproduktivität bei.
Definition
Die DIN 31051 definiert Instandhaltung als Oberbegriff, dem die Begriffe Wartung, Inspektion und Instandsetzung zugeordnet sind (Abbildung 13).
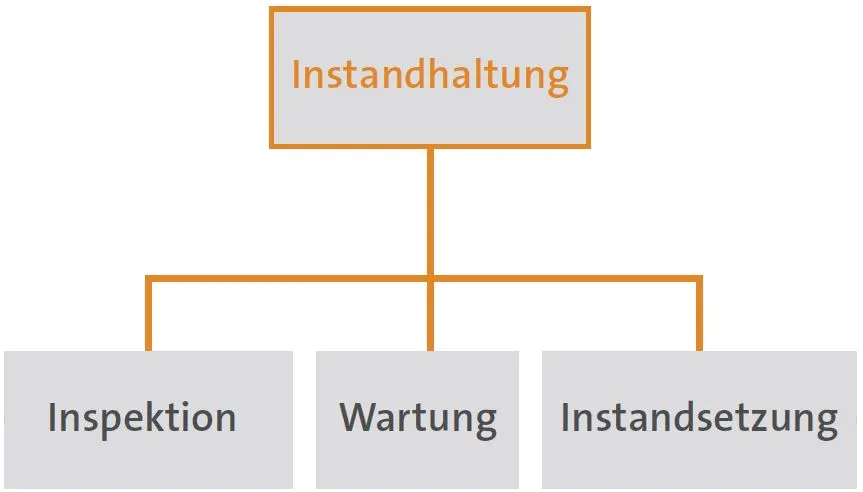
Die Instandhaltung umfasst alle „Maßnahmen zur Bewahrung und Wiederherstellung des Sollzustandes sowie zur Feststellung und Beurteilung des Istzustandes von technischen Mitteln eines Systems“ (DIN 31051).
Maschinen und Anlagen unterliegen durch ihren Gebrauch einem Verschleiß, der ihre Funktionsfähigkeit beeinträchtigt. Im Normalfall ist davon auszugehen, dass die Gesamtkapazität von Betriebsmitteln bei Inbetriebnahme 100 Prozent beträgt. Die Kapazität, die auch als „Abnutzungsvorrat“ bezeichnet wird, nimmt mit fortschreitender Nutzung immer weiter ab. Dem wirken die drei Teilbereiche der Instandhaltung entgegen:
- Erfassen des IST-Zustands durch Inspektion - Die Inspektion ist derjenige Teilbereich der Instandhaltung, der den Zustand der Betriebsmittel feststellt und mit dem SOLL-Zustand vergleicht, um Probleme (Schäden, Mängel) frühzeitig zu erkennen. Der Einsatz intelligenter Mess- und Analyseverfahren hilft Ihnen dabei, Störfälle sofort zu erkennen oder sogar auszuschließen, indem sie den Instandhaltungsbedarf rechtzeitig vor der Maschinenstörung oder dem Maschinenausfall entdecken.
- Bewahren des SOLL-Zustands durch Wartung - Unter Wartung sind die Aktivitäten zu verstehen, die durch regemäßige Pflege dem Verschleiß von Maschinen und Anlagen entgegenwirken.
- Wiederherstellen des SOLL-Zustands durch Instandsetzung - Die Instandsetzung umfasst alle Maßnahmen, die nach Eintritt und Feststellung einer Maschinen- oder Anlagenfunktionsunfähigkeit durchgeführt werden, um den ursprünglichen Anlagezustand wiederherzustellen oder zu verbessern.
Instandhaltung strategisch planen
Eine markt- und wettbewerbsorientierte Unternehmensstrategie verlangt hohe Verfügbarkeit und Zuverlässigkeit der kapitalintensiven Produktionsmaschinen und -anlagen. Umweltschutz- und Arbeitssicherheitsbelange erfordern hohe Maschinen- und Anlagensicherheit. Sie sollten deshalb die Instandhaltungsziele mit den Unternehmenszielen abstimmen und entsprechende Instandhaltungsstrategien und -konzepte festlegen.
Da das Reagieren auf Ausfälle und Störungen durch Reparaturen (Instandsetzung) nicht wirtschaftlich ist, empfehlen wir Ihnen, präventive Instandhaltungsmaß- nahmen zu planen. Eine präventive Instandhaltung legt entweder zustandsabhängige (leistungsbezogene) Instandhaltungszeitpunkte oder periodische Instandhaltungsintervalle fest.
Während die konventionelle Instandhaltung vorbeugend orientiert ist und mit festen Fristen (Prüfungen, Laufzeiten, Überholungen) ohne Berücksichtigung des Geräte-, Maschinen oder Anlagenzustands arbeitet, unterstützen die zustandsbedingten Instandhaltungsmaßnahmen folgende Ziele:
- Minimieren der planbaren, weil vorbeugenden Instandhaltung, mit der Sie ein technisches System in einem definierten SOLL-Zustand erhalten,
- Optimieren der nicht planbaren (korrektiven) Instandhaltung, mit der Sie den SOLL-Zustand eines technischen Systems wiederherstellen,
- Maximieren der zustandsüberwachenden Instandhaltung.
Im Gegensatz zu einer intervallabhängigen Instandhaltung wird ein Bauteil erst dann gewechselt, wenn der Abnutzungsvorrat zu 100 Prozent erreicht ist. Sie erreichen so eine maximale Nutzung der Lebensdauer. Ein weiterer Vorteil ist die terminabhängige Planung aufgrund von Erfahrungswerten. Dem stehen die Nachteile zusätzlicher Inspektionsmittel (bei komplexen Maschinen und Anlagen besonders hoch) für eine Dauerüberwachung und die damit verbundenen höheren Kosten gegenüber. Deshalb prüfen Sie, ob alternativ ein Stichprobenverfahren für Ihr Unternehmen beziehungsweise für eine bestimmte Fertigungsanlage oder -maschine in Frage kommt.
Strategische Ausrichtung der Instandhaltung
„Der Instandhaltungsprozess bewegt sich in seiner strategischen Ausrichtung üblicherweise im Dreiecksverhältnis reaktiver, präventiver und zustandsorientierter Maßnahmen [ . . . ]. Bei der reaktiven Instandhaltung steht die Funktionserhaltung durch ,Crashund Feuerwehreinsätze‘ im Vordergrund. Folgeschäden werden in Kauf genommen. Im Gegensatz hierzu steht die präventive Instandhaltung. Der Focus liegt in der Werterhaltung durch vorbeugenden Austausch verschleißanfälliger Teile. Restnutzungsmöglichkeiten werden nur bedingt ausgeschöpft. Beide Ansätze haben auch heute noch ihre Berechtigung. Die Grenzen werden jedoch immer fließender, durch die Anforderungen an eine zustandsorientierte Instandhaltung. Durch Inspektionen werden technische Veränderungen frühzeitig erkannt und Ursachenanalysen zeigen den Handlungsrahmen auf. In die Zukunft gerichtete Prognosen werden ermöglicht und Risiken sind kalkulierbar. In der Frage nach dem richtigen Strategiemix zeigt die Realität allerdings, dass der optimale Punkt nie wirklich erreichbar ist. Im Spannungsfeld zwischen zu viel und zu wenig, zwischen Kosten und Nutzen und zwischen Risiko und Sicherheit ändern sich die Rahmenbedingungen ständig. Die Strategie hat sich schlussendlich an den Gesamtkosten zu orientieren, die in Verbindung mit dem technischen Ausfall zu den wirklichen Betriebskosten führen.“ (Hodapp: Die Bedeutung einer zustandsorientierten Instandhaltung, S. 137)
Es kann aber keine allgemeingültige Empfehlung von Maßnahmen geben unabhängig von den konkreten betrieblichen Rahmenbedingungen, weil Sie das Verhältnis von Aufwand und Nutzen ständig optimieren. Wenn Sie zum Beispiel den Zeitbedarf für Instandhaltungsarbeiten auf das unumgänglich scheinende Maß reduzieren, kann das zu höheren Instandhaltungskosten führen.
Ausfallverhalten/-risiko von Maschinen und Anlagen optimieren
Das Ausfallverhalten von Geräten, Maschinen und Anlagen während ihrer Nutzungszeit lässt sich aufteilen in die Phasen des Früh-, Zufalls- und Spätausfalls. Frühausfälle weisen eine im Zeitablauf abnehmende Ausfallrate auf, die Ausfallrate der Zufallsausfälle ist zeitunabhängig, in der Spätausfallphase nimmt die Ausfallrate im Zeitverlauf zu. Tritt der Ausfall eines Bauelements in der ersten Phase seiner Lebensdauer auf, handelt es sich um einen Frühausfall. Ursächlich können Fehler bei der Projektierung, Konstruktion, Fertigung und Montage sein, aber auch fehlende oder unzureichende Qualifikation und Erfahrung des Bedienungspersonals. Vor allem bei Sonderlösungen (zum Beispiel Spezialmaschinenbau) ist das Ausfallrisiko hoch, da es hier keine länger dauernden Lernkurven gibt. Um die prinzipiell nicht auszuschließenden Frühausfälle zu reduzieren, legen Sie besonderes Gewicht auf die Planung der frühen Nutzungsphasen.
Die stabile Phase der sogenannten Zufallsausfälle können Sie dazu nutzen, die verschiedenen Formen des Verschleißes zu identifizieren und damit eine Vorhersage des Langzeitverhaltens der betreffenden Maschine zu treffen. Je präziser das gelingt, desto zielgerichteter kann dann in der Phase des alterungsbedingten Spätausfalls der rechtzeitige Austausch technisch abgenutzter Bauteile erfolgen. Ein erwünschter Effekt besteht in einem "kostenminimierbaren Ersatzteilmanagement, das teure Reserveteile auf den Punkt genau beschafft und nicht langjährig in ungenutzten Lagerbeständen bindet. So wird Instandhaltung zu einem Produktivitätsfaktor, indem das Risiko kalkulierbar wird und der technische Werterhalt gezielt bis hin zur definierten Nutzzeitverlängerung in Abgleich mit der Investitionspolitik erfolgen kann." (s. Hodapp, Die Bedeutung einer zustandsorientierten Instandhaltung, S. 141)
Sicherheits- und betriebskritische Ausfälle vermeiden
Um zu vermeiden, dass technische Defekte die Sicherheit der betrieblichen Abläufe gefährden, untersuchen Sie am besten, welche Arten von Ausfällen bei den eingesetzten Geräten, Baugruppen und Maschinen auftreten können, und legen fest beziehungsweise dokumentieren, welche Verfahren zur Störungserkennung und -behebung jeweils anzuwenden sind.
Grundsätzlich nutzen Sie zur Ausfallerkennung die Möglichkeiten der Inspektion, der wiederkehrenden oder permanenten Prüfungen und der automatischen Meldung. Zur Vermeidung sicherheits- und betriebskritischer Ausfälle empfehlen sich eine periodische oder permanente Zustandsüberwachung und Bereitstellung von Ersatzgeräten. Planen und dokumentieren Sie Maß- nahmen, die das Ausmaß von Schäden durch technische Störungen und Ausfälle begrenzen.
Soweit bei Störungen und Ausfällen keine sicherheitskritischen Funktionen betroffen sind, sind die herkömmlichen Maßnahmen der nicht planbaren (korrektiven) Instandsetzung geeignet.
Im Hinblick auf die automatisierte Meldung durch Fertigungsmesstechnik sollten Sie sicherstellen, dass die ermittelten Daten so ausgelegt, abgestimmt und bereitgestellt werden, dass sie zur Verbesserung sowohl des Instandhaltungs- als auch des Produktionsprozesses beitragen. Auch hier ist zu beachten, dass eine größere Mess- und Prüfgenauigkeit auch höhere Kosten verursacht und dass die messtechnische Genauigkeit zu den im Produktionsprozess geforderten Toleranzen passt, damit nicht „mit Kanonen auf Spatzen“ geschossen wird. Bei den kundenseitig geforderten Toleranzen dürfte heute allerdings in vielen Fällen das Gegenteil notwendig sein – das Management extrem niedriger Toleranzgrenzen.
Organisation der Instandhaltung
Die große Bedeutung der Instandhaltung resultiert aus der fortschreitenden Automatisierung der Fertigungsprozesse und der Notwendigkeit, die technischen Produktionskapazitäten optimal zu nutzen. Damit können Verfügbarkeits-, Auslastungs- und Qualitätsverluste eingeschränkt oder vermieden werden. Den komplexen Anforderungen einer zeitgemäßen Instandhaltung wird weder eine zentral noch eine dezentral (fertigungsintegrierte oder "autonome") organisierte Instandhaltung gerecht.
Da die Komplexität der industriellen Fertigungstechnologien weiter zunimmt, benötigen Sie zur Aufrechterhaltung Ihrer Produktionsprozesse hochqualifizierte Instandhaltungsspezialisten. Ob Sie diese per Eigenleistung realisieren, also mit eigenem Personal, oder per Fremdbezug durch Anlagenhersteller oder spezialisierte Dienstleister, ist eine wichtige Entscheidungsalternative, die aber nur betriebsindividuell vor dem Hintergrund von Unternehmenszielen, Instandhaltungsaufwand und Personalkapazitäten beantwortet werden kann.
Andererseits sind die Fertigungsmitarbeiter (Bedienungspersonal) mit den am Arbeitsplatz vorhandenen Maschinen und deren Schwächen so gut vertraut, dass eine ausschließlich durch Spezialisten betriebene Instandhaltung nicht immer sinnvoll erscheint.
"In vielen kleinen und mittleren Unternehmen übernehmen Mitarbeiter der Produktion die Instandhaltung und rufen erst dann den (externen) Spezialisten oder Reparaturservice, wenn die eigenen Möglichkeiten zur Fehlerbehebung ausgeschöpft sind. Durch zunehmende Automatisierung, Einführung von Prozessleitsystemen, komplexe Hydraulikanlagen etc. wurden zunehmend dezentrale oder zentrale eigenständige Instandhaltungsbereiche neben der Produktion aufgebaut. So entwickelten sich über viele Jahre in den meisten Unternehmen die beiden Funktionen mit getrennter Leitung und nicht selten auch mit unterschiedlichen Interessenlagen. Dem Kunden ist dies letztlich egal; sein Ziel ist es, dass die Aufträge bestmöglich hinsichtlich Kosten, Qualität und Termintreue erledigt werden. Daraus muss sich die betriebliche Gemeinschaftsaufgabe für Produktion und Instandhaltung entwickeln, Verfügbarkeit und Zustand der Anlagen zu optimieren, um Kundenzufriedenheit zu gewährleisten. Aus Sicht der Produktion entwickelt sich die Instandhaltung so vom ,notwendigen Übel‘ oder ,Helfer in der Not‘ hin zum ganzheitlichen Instandhaltungsmanagement, an dem Produktion und Instandhaltung gemeinsam Anteil haben." (Hans Böckler Stiftung (Hrsg.), Integration von Produktion und Instandhaltung, S. 9)
Prinzipiell kann die Instandhaltung als gesonderte Instandhaltungsabteilung, durch Teams aus Instandhaltungs- und Produktionsmitarbeitern oder autonom, das heißt produktionsintegriert organisiert sein (Abbildung 14). In der Realität wird man Überschneidungen und Mischungen dieser Basiskonzepte finden, die den jeweiligen betrieblichen Bedingungen entsprechen.
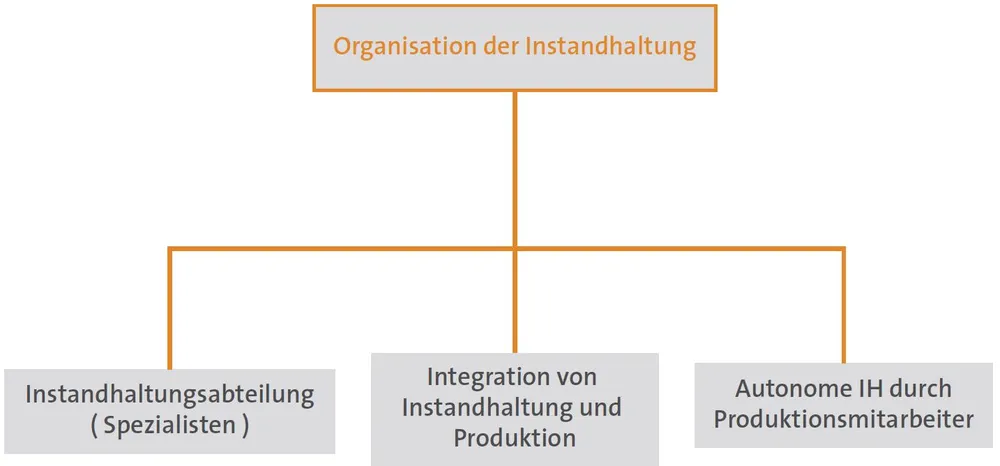
- © FabrikaCr / iStock.com – Header_Website_1460_360_magazin.jpg
- © RKW Kompetenzzentrum – 20151208-Abb.12-Produktivitaetswirkungen-des-Handlungsfelds-Instandhaltung.JPG
- © RKW Kompetenzzentrum – 20151208-Abb.13-Struktur-der-Instandhaltung.JPG
- © RKW Kompetenzzentrum – 20151208-Abb.14-Organisationsformen-der-Instandhaltung.JPG